First impressions on the CNC 3020
So, I ordered a CNC 3020T-DJ. Surprisingly, the "Free shipping" on the eBay item turned out to be UPS delivery, which only took 10 days to arrive from the day I ordered. Weight of the package was 22.5 kg, and I estimate that shipping was about 200 USD out of the 750 USD total cost.
Unpacking
The machine arrived in a box about 40x40x50 cm. The machine itself was at the bottom of the box, with two smaller boxes with the power supply and the motors above it.
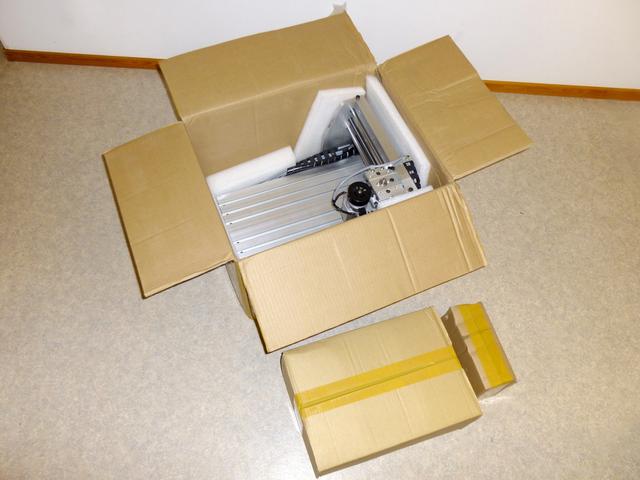
The only assembly necessary was to attach the three stepper motors. They attach each with 4 Allen screws and a small screw that tightens the coupling.
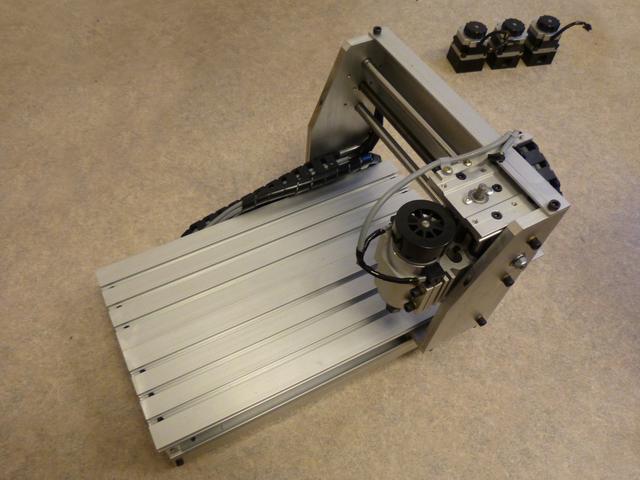
Spindle
The spindle and its motor plays a very important part in the accuracy and performance of CNC mills. It's speed range largely determines what kind of tools can be used and what materials can be milled. Too high a speed will cause many plastics to melt and cause difficulties with larger tools. Too low power and metals will be out of reach.
Another important part is the runout of the spindle. This means both the eccentricity and alignment error in the axis, i.e. how much the tool wobbles when spinning. A high runout will break small tools and drills. Finally, the play in the spindle bearings can limit the milling accuracy, as the axis will deflect when there is a load where the tool hits the material.
The spindle in CNC 3020 has a 48 volt 200 watt DC spindle motor. The controller it comes with can adjust the speed from about 300 to 10 000 RPM, but does not actually regulate the speed. Adding a feedback loop could help when using smaller rates, as with open-loop PWM adjustment the power of the motor drops at low speed settings.
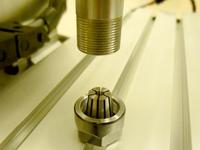
Tools are attached to a 3.2 mm collet, which is the same as used on most Dremel tools. Great, as this means I can easily use the same tools on both.
In order to estimate the rigidity and runout of the spindle, I mounted a 0.2 mm drill bit on it and recorder a microscope video, shown below.
Not surprisingly, there is significant play in the spindle. Using the totally scientific method of applying exactly 10 Newtons of force by hand, I estimate the play to be about ± 0.2 mm. This is not particularly great, but in line with the price of the machine. However, the runout is somewhat more difficult to estimate from the video, as the spiral shape of the drill bit changes its appearance depending on how light hits it.
To better estimate the runout, I mounted a tool backwards and shone a flashlight on the round shaft so that a thin strip of light was visible at the edge. Then I used a small Python script to calculate the position of the shaft in each video frame:
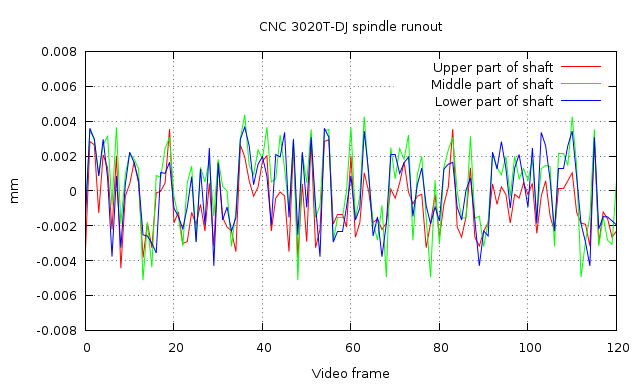
There is a lot of noise, and the method is probably not very accurate. However, it seems that the total indicated runout is somewhere around 0.004-0.010 mm, or 0.0004 inch. This is a pretty good result for such a cheap machine, and should not limit my tool choices at all.
One thing that sticks out is that the spindle is really quiet, atleast compared to my Dremel. You can barely hear it a few meters away when it is running at 5 000 RPM without load. At highest speed settings the fan at the top will start to make some noise, though.
Rigidity of the frame
When milling harder materials, the rigidity of the frame and slides often limits the accuracy that can be reached. The CNC 3020 has a moving gantry, with two round steel shafts and one trapezoid thread for each axis.
In the video below, I tug at the frame from various points with a force of about 10 Newtons. Especially the top of the gantry flexed a lot, but because the tool is much closer to the table the movement is not so large at that point.
Again, there is about ± 0.2 mm of flex. Combined with the play in the spindle, this comes up to ± 0.4 mm, which starts to be a bit problematic for more precise operations. However, if one keeps the depth of cut small, the forces will not be that great.
Work table
The work table is made out of an aluminum profile with 7.5 mm slots every 30 mm. The machine came with some 6 mm bolts and square nuts that fit the slots, but that didn't seem very convenient. Instead, I noticed that 6 mm carriage bolts work perfectly for the purpose, and with some wing nuts are also easy to attach.
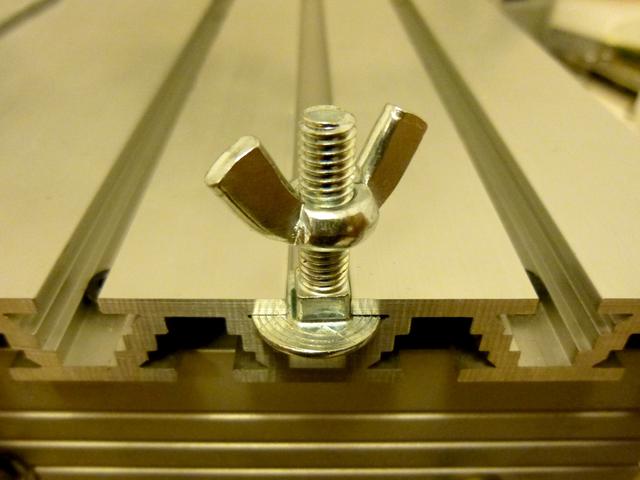
Overall
It seems like a suitable machine for my purposes, and is probably of higher quality than that of Shapeoko 2, which is in the same price range. Of course the design is not as open, and availability of spare parts may be worse. However, replacing the electronics with a Smoothieboard will improve the hackability a lot, so perhaps it'll also function as a 3D printer or even a laser cutter.
I don't yet have a way to drive it, as the original control box needs a parallel port on PC. I have made a few test cuts manually, and the surface quality seems relatively good. Acrylic and polycarbonate mill really well, and brass seems doable also. It was even able to make a groove in a steel washer, but the spindle flexes so much that the it's not really feasible to do any accurate work on steel.
– Petteri Aimonen on 9.3.2014