Smoothieboard conversion
The original electronics on CNC3020 are a blast from the past. Designed to be driven from a parallel port using realtime PC, it has just three TB6560AHQ stepper drivers and a big heatsink. I didn't feel like having a desktop PC just for this, so I replaced the driver board with a Smoothieboard.
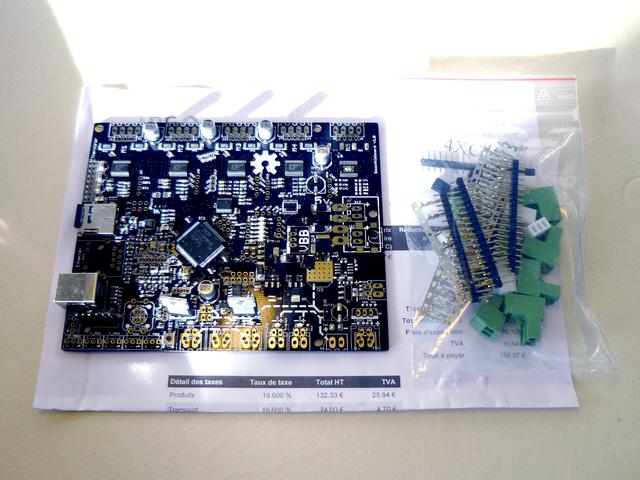
Smoothieboard makes the device completely autonomous, so that you can just select a file to run and leave it running without a computer attached. Of course it also supports live feeding of G-code over USB bus.
Chassis mod and wiring it up
Cutting a few new holes (for USB and SD card) to the back panel was a quick job with Dremel. Also needed to solder new internal wiring, which didn't end up quite as neat as the original but is good enough for me.
I wanted to use a LCD screen with the Smoothieboard, so I needed to redo the frontpanel also. This was somewhat more difficult, as it would have to be good looking also.
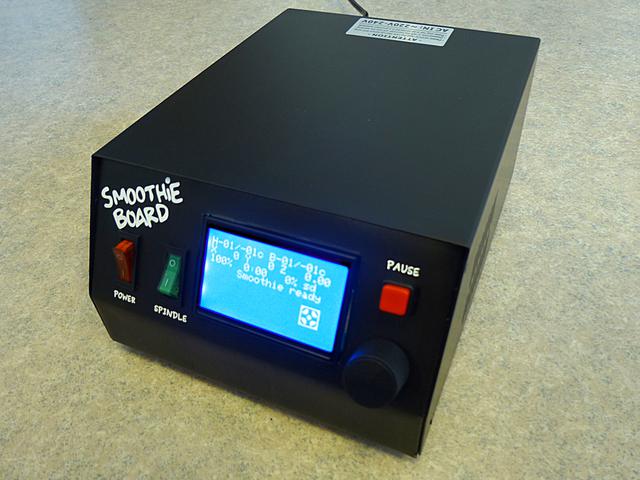
Surprisingly, double-printing a sheet of photo paper on my laser printed gave a very nice black surface. The texts in the above photo are the only places without toner, everything else is covered by a nice thick layer of it. The photo paper is spray glued to the box front panel, where it covers the old holes and texts.
Trying it out
The first pieces I machined were some fasteners for a gym bar. Immediately it was obvious that there is more to machining than just pressing "Go".
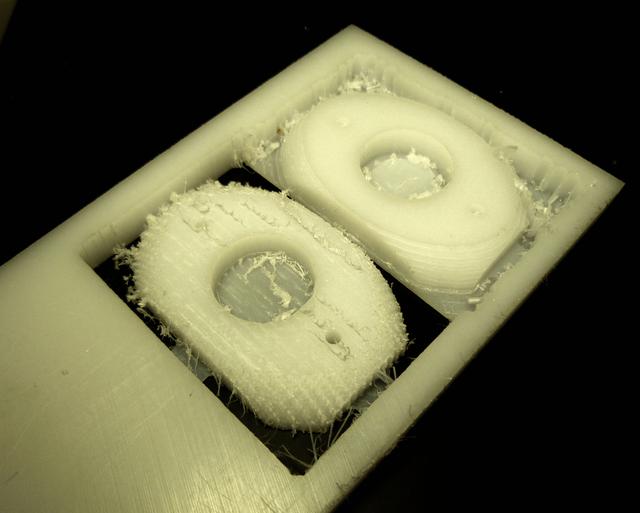
With an unsuitable endmill, the polycarbonate material leaves a very fuzzy surface. Also the milling direction affects the end result a lot. Still a lot to learn, but the results were usable if not very pretty.
A second test piece in wood succeeded much better.
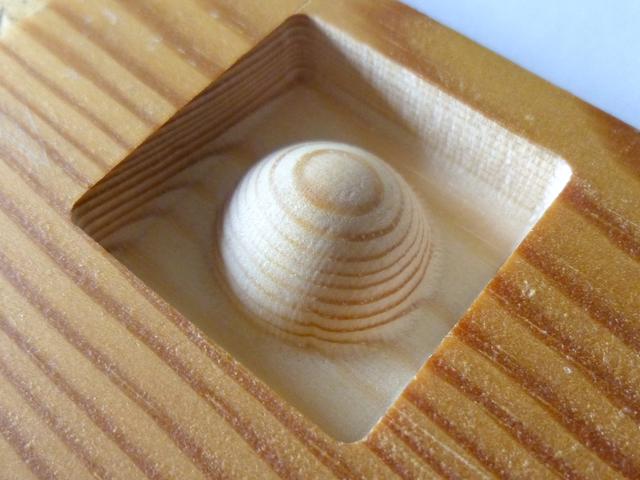
If your browser does not support WebM for video, you can either watch on YouTube or download the video.
The 2 cm diameter semisphere was designed in OpenSCAD and the toolpath made using PyCAM. Seems like most open-source CAM tools (I have tried PyCAM, MakerCAM and BlenderCAM) are still a bit buggy at places and produce quite inefficient toolpaths, but overall they get the job done. Buying a license to CamBam might be a good idea, or perhaps I'll be able to improve the open source tools.
I also tried out some aluminum machining by making a few workpiece mounting bars:
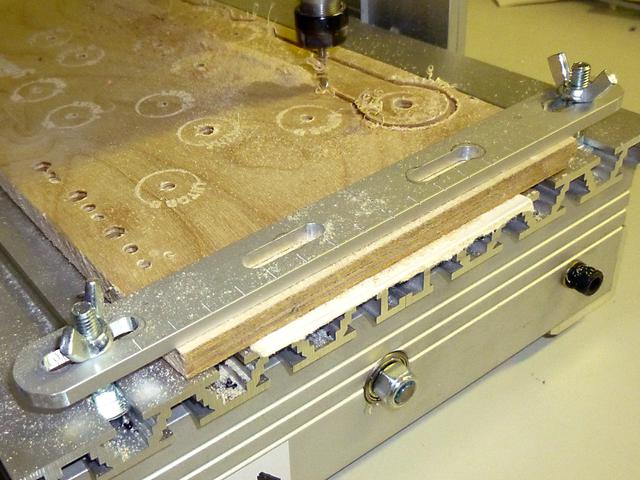
That went quite well also, though the mill seems to be prone to some resonances. At poor feed / overstep / step down combinations, the whole spindle starts to vibrate, ruining the surface quality completely.
– Petteri Aimonen on 29.6.2014